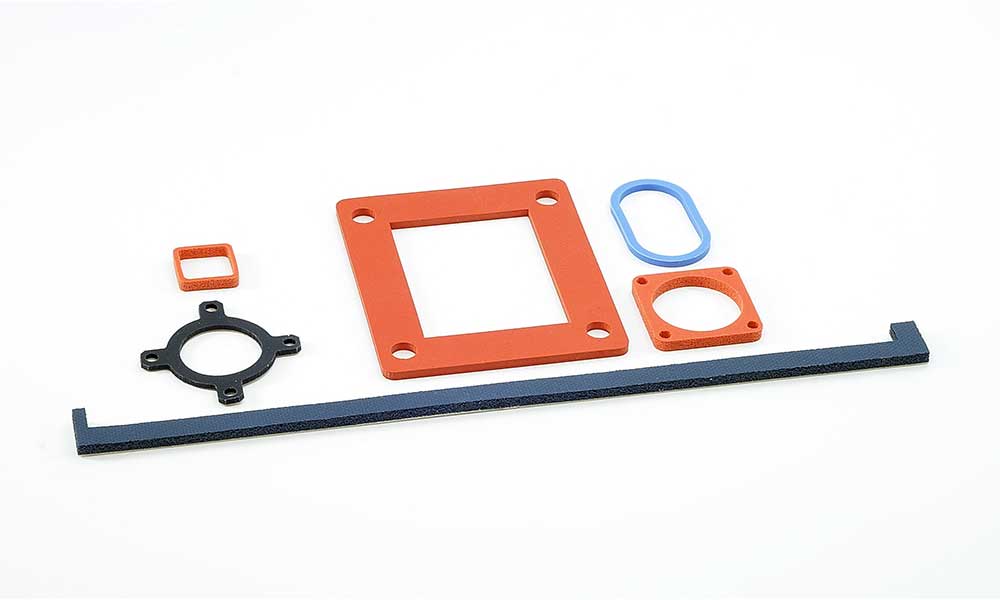
Stockwell Elastomerics manufactures custom high temp gaskets from various high temperature gasket materials to customer specifications.
“High temperature” is a relative term as it pertains to gaskets and seals. Metallic and composite seals can withstand temperatures well above 1000°F. Elastomeric or rubber gaskets on the other hand have much lower operating temperature; an operating temperature above 350°F (177°C) is considered high temperature for polymers. High heat gaskets and heat resistant gaskets are other names for a high temperature gaskets.
Custom High Temperature Gaskets
Stockwell Elastomerics works with customers to provide custom high temp gaskets and pads based on the specific application and environment where they will be used. Material selection and the manufacturing process are critical for the gasket to maintain integrity in high heat applications, and other environmental factors must also be considered too. While the temperature range may be the most critical consideration, the material’s compressibility, durometer, and durability are important considerations, along with other potential factors such as EMI or ESD protection, vibration dampening, cushioning requirements, and resistance to water, oil, fuel or chemicals, to name a few. Stockwell Elastomerics’ Applications Engineers have vast experience in providing assistance to customers seeking high temperature gaskets to function in various environments for long life and failure prevention.
Why Use High Temperature Gasket Material?
Environmental conditions should always be considered when designing an elastomeric gasket or cushioning pad. Excessive heat will gradually degrade rubber materials as well as deteriorate performance. As a precursor to many rubber tests, heat aging of the rubber material prior to mechanical testing is typical; ASTM D 573, ASTM D 1056, UL 50, UL 48, UL 508, and UL 157 have heat aging requirements. Gaskets and pads exposed to high temperature or prolonged heat exposure can exhibit premature failure leading to water ingress.
Heat Aging Examples for High Temperature Gasket Materials
Specification | Test Criteria | Conditions |
---|---|---|
ASTM D 1056 | Compression Deflection | 168 hrs @ 158°F (70°C) / 22 hrs @ 302°F (150°C) |
ASTM D 1056 | Compression Set | 22 hrs @ 158°F (70°C) / 22 hrs @ 212°F (100°C) |
UL 48 (signs) | Tensile or elongation | 70 hours @ 212°F (100°C) |
UL 48 (signs) | Visual (cracking after flexing) | 70hrs @ 212°F (100°C) |
UL 50 (enclosures) | Tensile and elongation | 168 hours @ 158°F (70°C) |
UL 157 (gasket and seals) | Tensile and elongation | 70 hours @ 212°F (100°C) |
UL 508 (industrial controls) | Tensile and elongation | 70 hours @ 212°F (100°C) |
Heat Survival vs. Functionality – Heat Influence on Rubber
Surviving a heat aging test only tells part of the story. Many of the heat aging tests look at tensile and elongation as indicators of permanent deformation, they are indicators of how the polymer is influenced by high temperatures. While some materials will pass the heat aging tests, a significant number of materials will not perform as well in applications due to the duration of heat exposure. Often long term exposure to elevated temperatures that are not as hot as testing temperatures will cause materials to take a compression set or relax. Stress relaxation describes how “push back” of the gasket is reduced. This push back is critical to seal out rain and pressure washing.
Important: When comparing compression set properties take note of the test temperature. Many organic rubber materials are tested at ambient (73°F), and most of these will take a permanent set at elevated temperatures.
Commercially Available High Temp Gasket Materials
The high temperature limit for most commercially available “rubber” products is below 500°F (204 – 260°C); silicone rubber inherently has the best temperature stability of these. The standard operating temperature for silicone ranges from 400 – 500°F (204 – 260°C) with intermittent temperature up to 600°F (333°C). Other materials such as fluorocarbon, EPDM and fluorosilicone have good to excellent heat resistance. This means the gasket material maintains its mechanical properties and will continue to perform as designed without reversion.
Flame Rated Gaskets vs. High Temperature Gaskets
Customers often require gaskets to carry flame ratings – an example is UL 94. Although silicone is generally a high temperature elastomer, this does not always correlate to a flame rating. Silicone foams often carry UL 94V-0 flame ratings, although their high temperature range is lower than that of a silicone sponge. UL 94V-0 flame ratings allow a material to burn and measure time to extinguish and types of “dripping” particles.
Flame temperatures far exceed the operational temperature limit of any silicone. Once flames are involved, the concern is about extinguishing and limiting spread. For more information on this topic, visit the UL 94 Flame Rated Gaskets page.
General Operating Temperatures for Common Rubber Materials*
- Silicone: 400 – 500°F (204 – 260°C)
- Fluorocarbon: 400 – 500°F (204 – 260°C)
- Fluorosilicone: 400 – 500°F (204 – 260°C)
- EPDM: less than 400°F (204°C)
- Nitrile (Buna-N): less than 300°F (149°C)
- Chloroprene (Neoprene): less than 300°F (149°C)
- Natural Rubber: less than 250°F (121°C)
- Urethane: less than 250°F (121°C)
* Temperatures ranges are approximate; values will vary with grade. Refer to material specifications for actual product temperature ratings.
Silicone, fluorocarbon, fluorosilicone and EPDM are considered high temperature rubber materials and are readily available in sheet stock form (solid silicone sheet, closed cell sponge, and open cell foam). Silicone may also be injection molded or compression molded in various hardnesses, from as low as 10 durometer to 80 durometer on the Shore “A” scale. If very low temperatures are required, silicone or fluorosilicone would be the best choice. Fluorocarbon and fluorosilicone are generally readily available. However, these materials are typically more costly specialty products used where chemicals and fuels are present.
Frequently Asked Questions About High Temperature Gaskets
Q: The datasheet for HT-800 shows a high temperature that is different than R10470M. Why the difference if they are both silicone?
A: HT-800 is a liquid-based silicone product. This means that is has some slightly different properties when compared to a gum-based silicone like R10470M. High temperature resistance is an example of a property that varies between these two materials. Contact Stockwell Elastomerics’ Applications Engineering team for help selecting the appropriate solution in situations like this.
Q: What happens to silicone if the material is exposed to temperatures over its listed operational range?
A: That depends. For a very short term (seconds, minutes, hours) exposure to a temperature that is slightly over, no major effects are expected. However, longer term exposure (days, weeks) will begin to degrade material properties such as tensile, compression set, and compression force deflection. This can cause a gasket to no longer function as expected.
Q: How can silicone foam be UL 94V-0 rated if it has a high temperature range of 392 degrees Fahrenheit?
A: No silicone product can truly survive a flame – the temperature is too great. However, silicone foams have the ability to self-extinguish when exposed to a flame. The UL 94V-0 rating categorizes how quickly the material self extinguishes. However, a flame-burned silicone gasket is no longer functional. Temperature ranges on these materials are all about the limits of functionality. Temperature ratings show how hot a material can get while still working as expected. Flame ratings show how materials deal with fire, but do not involve functionality or performance after.
Contact Stockwell Elastomerics for High Temperature Gaskets and High Temp Gasket Material
Contact us for further assistance with custom high temp gaskets, high heat gaskets, heat resistant gaskets, and high temperature gasket materials.